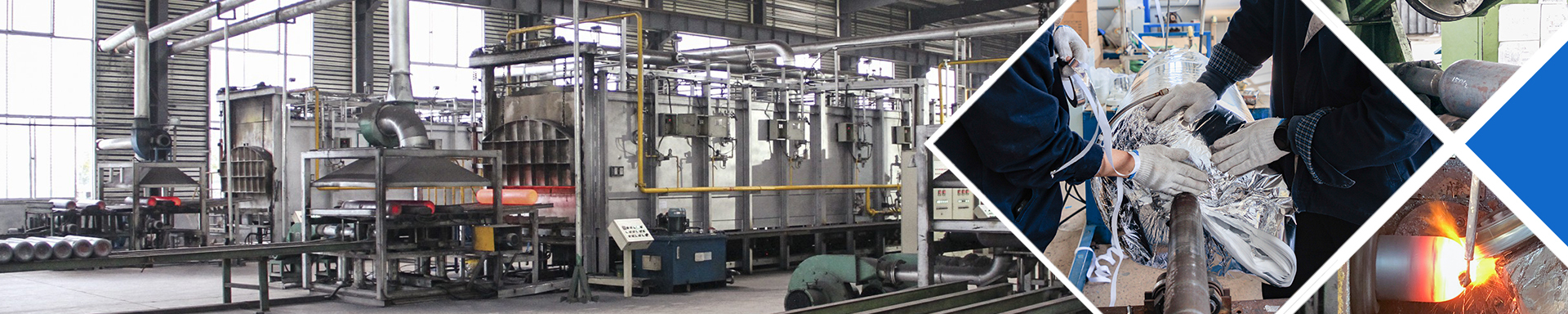
The Producing Process of Welding Cylinder
A welding cylinder is a container used to store compressed gases such as oxygen, acetylene, argon, and helium used in welding and cutting applications. This container is made of sturdy materials such as steel or aluminum and can store these gases at high pressures. Welding cylinders come in various sizes and shapes and are designed to withstand the pressure and impact of welding operations.
The production process for welding cylinders involves several stages of fabrication and assembly to create a robust, reliable container that can hold compressed gases safely. This process typically starts with the selection of high-grade materials such as steel or aluminum that can withstand high pressures and impact.
In this video, we take the viewers through the various stages involved in the production process of welding cylinders. It showcases the different types of machines and tools used at each stage, the materials used, and the safety protocols in place.
The first stage of the process involves the cutting and shaping of metal sheets into the appropriate dimensions of the cylinder. The sheets are then formed into a cylindrical shape using specialized machinery that ensures accuracy and precision.
The next stage involves the welding of the seams to create a sturdy, leak-proof cylinder. The presenter explains the different welding techniques used, including gas tungsten arc welding (GTAW) and gas metal arc welding (GMAW), and how skilled welders ensure the quality of the welds.
Once the cylinder is welded, it undergoes quality checks to ensure its integrity, such as pressure testing, leak detection, and visual inspection. Any defects are identified and corrected promptly to ensure that the finished product meets the required standards.
Finally, the cylinder is coated to prevent corrosion and give it a clean finish. The coating process involves surface preparation, primer application, and finishing with a durable, protective paint.