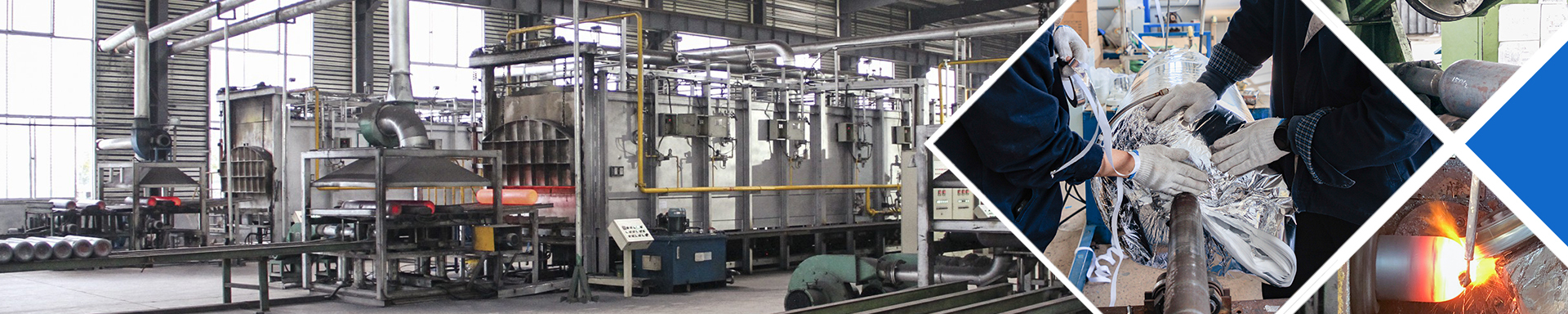
The Introduction to Producing Process of Seamless Cylinder
Seamles cylinders are high-strength containers that are used for the storage and transport of compressed gases such as oxygen, carbon dioxide, and nitrogen. Unlike welding cylinders, seamless cylinders are produced without any seams, making them stronger and more durable. They are used in a variety of industries such as healthcare, automotive, aerospace, and industrial manufacturing.
In medicine, seamless cylinders are used for the storage and transport of medical gases such as oxygen and nitrogen, which are critical for the functioning of healthcare facilities and emergency services. In the automotive industry, seamless cylinders are used for the storage and distribution of compressed natural gas (CNG), which is a cleaner and more efficient alternative to gasoline and diesel fuels.
In aerospace, seamless cylinders are used for the storage of gases used for rocket propulsion. The high-strength material and superior manufacturing process of seamless cylinders make them ideal for the demands of space travel.
In industrial manufacturing, seamless cylinders are used for the storage and transport of a wide range of gases used in welding, metal fabrication, and chemical processes. They are designed to withstand high pressure and extreme temperature environments, making them indispensable for industrial operations.
The production process for seamless cylinders involves several stages of precision engineering to create a strong, reliable container that can store compressed gases safely. Unlike welding cylinders, seamless cylinders are produced without seams or joints, which makes them more durable and less prone to leaks.
The first stage of the process involves the selection of high-grade materials such as steel or aluminum, which are then heated and formed into a hollow tube using specialized machines called piercers. The piercing process creates a long tube with a uniform thickness and diameter, which is then cut to the appropriate length.
The next stage involves the drawing process, where the tube is passed through a series of rollers and mandrels to reduce its diameter and increase its length. This process results in a seamless cylinder with a smoother and more uniform finish.
Once the drawing process is complete, the cylinder undergoes heat treatment to improve its strength and durability. The cylinder is then cleaned and inspected thoroughly using various non-destructive testing techniques to detect any defects or anomalies that could affect its performance.
Finally, the cylinder is coated with a protective layer to prevent corrosion and damage to the surface. The coating process involves surface preparation, primer application, and finishing with a durable paint.